The Greatest Guide To Premier Aluminum Llc
Table of ContentsNot known Incorrect Statements About Premier Aluminum Llc The Best Guide To Premier Aluminum LlcPremier Aluminum Llc Things To Know Before You BuyPremier Aluminum Llc Things To Know Before You Buy
(https://papaly.com/categories/share?id=8427583a7a0b4605874aa90ef65d4caf)Making use of low cost and unqualified distributors can cause quality issues, and threw away time and money in the lengthy run. To aid you via the process, below are some points to take into consideration when picking the right steel spreading provider.
A business that just makes use of the investment casting process will certainly try to offer you on why that procedure is best for your application (Casting Foundry). What if making use of the sand spreading procedure is best for you and your requirements? Rather, search for a vendor that supplies a variety of casting procedures so the best alternative for YOU is selected
If collaborating with a single source for all of your casting needs is necessary to you, the supplier needs to be varied in its capabilities. When incorporated with other incorporated capacities, this can assist streamline and press the supply base. When selecting the appropriate casting vendor, careful factor to consider should be provided to quality, solution, and rate.
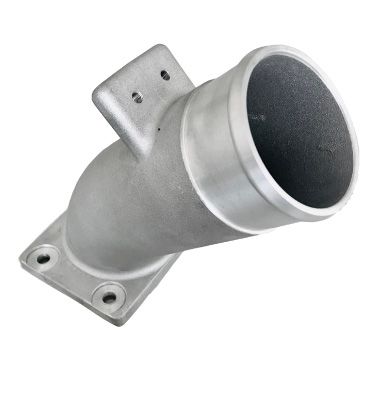
The Greatest Guide To Premier Aluminum Llc
Customers significantly choose casting distributors who have machining abilities. If the casting vendor discovers an issue during machining, the problem is resolved much faster with no conflict over whose fault it is.
What do you require from your spreading vendor? Are you looking for somebody to simply supply a steel component to your doorstep or do you require more?
Some factories are minimal or specialized. Make sure the supplier can satisfy all your product or alloy requirements to eliminate the requirement for numerous suppliers.
The Best Guide To Premier Aluminum Llc
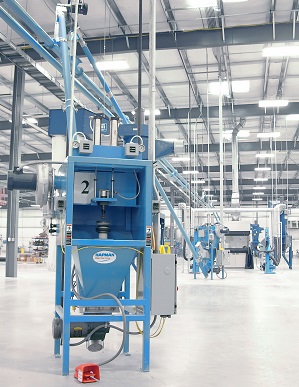
Study the distributor's internet site. Talk with a sales representative or organization affiliate. Ask a great deal of concerns. Visit their center. Obtain an understanding of what they can do for you and if you can see on your own developing a strong, common partnership with them.
Light weight aluminum is also lightweight and has excellent deterioration resistance, making it suitable for applications where weight and longevity are vital aspects. Additionally, light weight aluminum casting is a cost-efficient approach of production, as it requires much less power and sources than various other approaches. Iron spreading, on the various other hand, entails pouring liquified iron into a mold and mildew to produce a desired shape.
The Best Strategy To Use For Premier Aluminum Llc
Iron casting is likewise able to endure heats, making it appropriate for usage in applications such as engine parts and industrial equipment. Nonetheless, iron casting can be much more expensive than light weight aluminum casting due to the higher expense of basic materials and the power required to melt the iron. When deciding between aluminum casting and iron casting, it is very important to take into consideration the specific needs of the application.
If strength and resilience are more vital, iron casting may be the better option. Other elements to think about include cost, production volume, and lead time. Finally, both aluminum spreading and iron spreading have their own one-of-a-kind benefits and negative aspects. By meticulously taking into consideration the details demands of the application, makers can choose the best procedure for their product.ZheJiang Dongrun Casting Market Co,. Ltd was constructed in 1995, We have actually remained in the casting industry for more than 25 years. Pass away casting is the name given to the
process of developing intricate metal components through use molds of the component, additionally called dies. The process makes use of non-ferrous metals which do not include iron, such as aluminum, zinc and magnesium, as a result of the desirable properties of the steels such as low weight, higher conductivity, non-magnetic conductivity and resistance to deterioration. Die spreading manufacturing is quick, making high production degrees of components easy.
It generates more components than any kind of other process, with a high level of accuracy and repeatability. To find out more about die spreading and pass away spreading products utilized in the process, reviewed on. There are three sub-processes that drop under the category of die spreading: gravity die spreading (or long-term mold and mildew casting), low-pressure die spreading and high-pressure die casting. The pure steel, also called ingot, is included in the furnace and maintained the molten temperature of the steel, which is then movedto the shot chamber and injected into the die. The stress is after that preserved as the steel solidifies. When the steel solidifies, the cooling process starts. The thicker the wall surface of the part, the longer the cooling time due to the amount of interior steelthat additionally needs to cool down. After the part is totally cooled, the die cuts in half open and an ejection mechanism pushes the element out. Adhering to the ejection, the die is closed for the next shot cycle. The flash is the added material that is cast during the process. This should be cut off making use of a trim device to
leave simply the main element. Deburring removes the smaller sized items, called burrs, after the cutting process. The component is polished, or burnished, to provide it a smooth surface. Nonetheless, this proved to be an unreliable examination, due to the fact that the tester could cut into a piece and miss a location with porosity. Today, leading manufacturers use x-ray testing to see the entire interior of components without cutting into them. This allows them to more accurately accept or decline components. To reach the finished product, there are three key alloys utilized as die casting material to select from: zinc, light weight aluminum and magnesium. Zinc is among the most used alloys for die spreading as a result of its reduced expense of raw materials.